「めっき処理ってどんな工程があるの?」
「前処理や後処理は何をする?」
「めっきの種類によって工程が違うの?」
このような疑問を解決します。
こんにちは。機械設計エンジニアのはくです。
2019年に機械系の大学院を卒業し、現在はメーカーで機械設計エンジニアとして働いています。
本記事では、めっき学習の第3ステップとして「めっきの前処理と後処理」を解説します。
この記事を読むとわかること。
- めっき処理の工程がわかる
- めっきの種類ごとの工程の違いがわかる
- めっき部品を設計する際の注意点がわかる
前回の記事でめっきの具体的な方法を紹介しましたが、材料を準備したらいきなりめっきをして終わりというわけではありません。
脱脂洗浄や酸洗浄など材料の汚れを除去する前処理、めっき後の変色防止や耐食性向上のための後処理が必要になります。
とくに、めっき不良の原因は7〜8割が前処理と言われるほど、前処理は重要な工程。
今回は、そんなめっきの品質を左右する前処理と後処理をわかりやすく解説します。
めっきの工程について勉強したい方は、ぜひ参考にしてください。
めっき処理の工程
めっきの工程は、材料やめっきの種類によって異なりますが、一般的な流れは下記のとおり。
- 前作業・・・素材加工、治具取り付け、マスキングなど
- 前処理・・・電解洗浄、脱脂洗浄、酸処理など
- めっき・・・亜鉛めっき、ニッケルメッキ、クロムめっきなど
- 後処理・・・クロメート処理、変色防止処理など
- 後作業・・・熱処理、検査、梱包など
前作業や後作業は、めっき以外の機械加工でも行われる工程です。
部分めっきのためのマスキングは、めっきなどの表面処理でよく使われる方法。
具体的には、めっきしたくない部分を治具などで覆って、めっきされないようにすることです。
一方で、前処理や後処理はめっき特有の工程。
部材やめっきの種類によって処理内容が異なるので、以下で詳しく説明していきます。
めっきの前処理
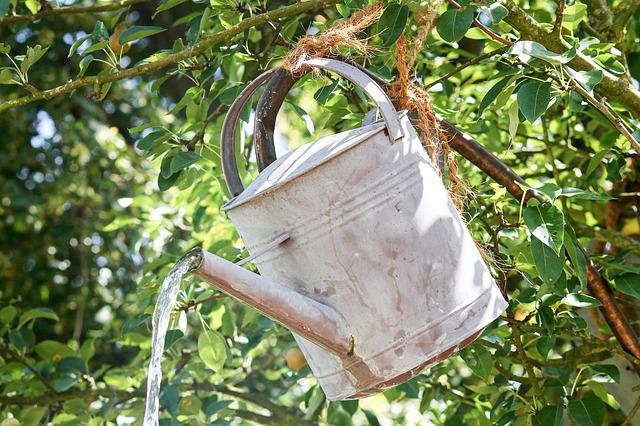
前処理は、素材表面の汚れを除去し、めっきの密着性を良くするための工程です。
素材表面が錆びていたり、油分がついていると、めっきの密着性が悪く、上手くめっきされません。
そこで、酸洗浄や脱脂洗浄によって汚れを除去し、めっきの密着力を確保するのです。
もちろん、材料によって性質や表面の状態は違うので、適切な洗浄処理を選択することが大切。
そのためには、材料に関する知識と経験が求められます。
脱脂洗浄
脱脂洗浄は、字のとおり油汚れを取り除くための洗浄です。
たとえば、スマホの画面を手で触ると指紋が付きますよね。
これは、指に付着している油分でスマホの画面が汚れているということです。
機械部品では、加工の際に潤滑油として油を使うので、部材表面には油脂分が付着しています。
この油脂分がめっきの「ノリ」を悪くするので、脱脂洗浄で取り除いてあげる必要があります。
ちなみに、主な脱脂洗浄は以下のとおり。
汚れの主成分によって、どの洗浄方法を使うかがわかれます。
- 溶剤脱脂・・・有機溶剤による脱脂
- アルカリ脱脂・・・アルカリ塩を複数組み合わせ、けん化作用によって脱脂
- エマルション脱脂・・・エマルション(有機溶剤と水が乳化した状態)による脱脂
- 電解脱脂・・・溶液に電解をかけて発生するガスの作用で脱脂
酸洗浄
酸洗浄は、金属のサビや酸化膜を除去する洗浄です。
一般的に、金属は酸素と反応しやすいため、通常、その表面は酸化膜で覆われています。
めっきのノリを良くするためには、酸処理によって表面の酸化膜を取り除き、生肌を露出させる必要があります。
薄いサビやスケール(水垢)の除去には塩酸を用いた酸洗いが、酸化膜や不活性物質の除去には酸電解処理や酸浸せき処理が用いられます。
- 酸洗い・・・薄いサビやスケールの除去
- 酸電解処理・・・強固に付着した酸化膜の除去
- 酸浸せき処理・・・脱脂や酸洗い後の、薄い酸化膜や不活性物質の除去
- 酸中和・・・表面に残留しているアルカリを中和して洗浄性を上げる
- 化学研磨・・・銅や黄銅の表面に強固に付着した酸化膜の除去
- エッチング処理・・・プラスチック、セラミックの密着強度を向上させる
水洗
めっきは、間をおくと表面に酸化膜が生じ、密着不良などの要因になります。
そのため、各工程は間をおかず連続的に処理されますが、この各工程間で行われるのが水洗です。
水洗の目的は、処理液を次工程に持ち込ませず、清浄な表面で各処理液と反応させること。
水洗が不十分だと表面に処理液が残ったままになってしまいます。
また、反対に水洗時間が長すぎると、酸化膜が発生してめっきの密着性が悪くなってしまいます。
したがって、水洗では処理液が完全に水に置換されるよう時間管理が重要になります。
めっきの後処理
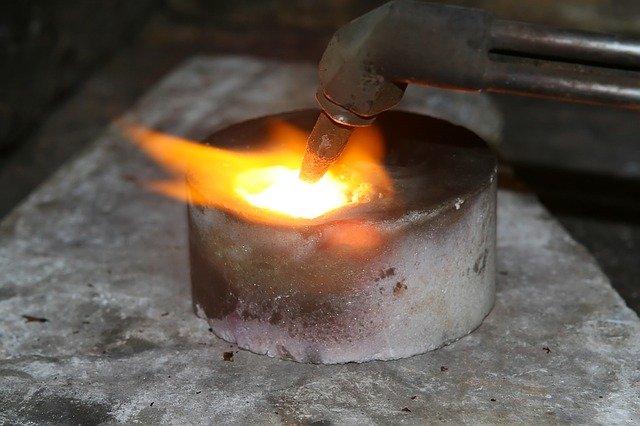
めっきの後処理の目的は、めっきの密着性向上、変色防止、被膜欠陥の補修、耐食性向上などです。
たとえば、銅や銀めっきは変色しやすいため、クロメート処理やクリア塗装などの変色防止処理が行われます。
具体的には、安定な極薄膜をめっき表面に形成させて、変色の原因となる酸素や塩素などの化合物がつかないようにする処理です。
また、亜鉛めっきやクロムめっきの水素ぜい性除去、無電解ニッケルめっきの密着性向上を目的として、熱処理を行うこともあります。
めっき部品を設計する際の注意点
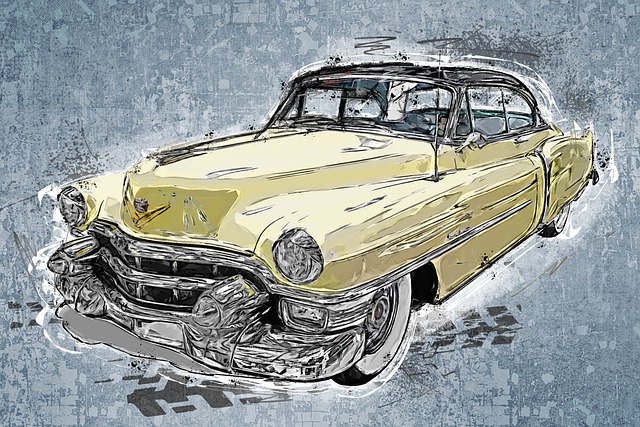
さいごに、めっき部品を設計する際の注意点・ポイントについて解説します。
設計時のポイント
めっき部品の設計では、下記の2点に注意します。
- めっきしやすい素材を選ぶ
- めっきしやすい形状にする
前回の記事で説明しましたが、電気めっき・無電解めっきは、イオン化傾向が大きい金属ほどめっきしにくくなります。
そのため、めっきではまず第一に素材選びが重要。
めっきしにくい材料を選んでしまうと、前処理や洗浄で対策が必要なため、難易度もコストも上がってしまいます。
また、部品の形状もめっきしやすさ・しにくさに影響します。
具体的には、たとえば曲げRは大きいほどめっきしやすいですし、複雑な形状だとめっき厚さのコントロールが難しくなります。
したがって、設計段階では不要な曲げや段付き形状は避ける、めっき可能かどうかわからない形状は逐一めっきメーカーに確認するなどの作業が必要です。
図面指示のポイント
めっき品を設計する際には、最低でも以下の3点を図面で指示する必要があります。
- めっきの種類
- マスキング
- 引っ掛け穴位置
マスキングとは、前半でも説明したとおり、めっきしたくない部分を治具などで覆ってめっきされないようにすることです。
たとえば、ねじ穴をめっきしたくない場合は、キャップでマスキングをしてめっき液が入らないようにします。
また、大きい部品のめっきには引っ掛けめっきと呼ばれる方法がよく用いられます。
具体的には、部品を治具に引っ掛けて吊り下げ、めっき液に浸せきするという手法です。
この場合、部品には引っ掛けるための穴を設ける必要があり、もともと穴がある形状であればその位置を引っ掛け穴として図面に指示します。
まとめ:前処理と後処理がめっきの品質を決める
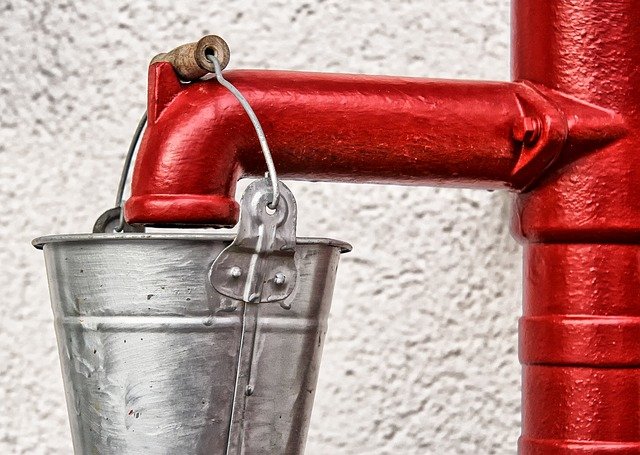
記事の内容をまとめます。
- めっきの工程は、前作業・前処理・めっき・後処理・後作業の5つにわかれる
- 前処理は、素材表面の汚れを除去し、めっきの密着性を良くするための工程
- 脱脂洗浄や酸処理などによって、素材表面に付いた汚れを取り除く
- 後処理は、めっきの密着性向上、変色防止、耐食性向上などを行う工程
- 各工程間では、水洗で処理液を除去する必要がある
- めっき品の設計では、めっきの種類・マスキング・引っ掛け穴位置の3つを図面で指示する
以上です。
今回は、めっきの工程として前処理と後処理について解説しました。
冒頭でも言ったとおり、めっき不良の原因の7〜8割は前処理にあると言われるほど重要な工程です。
めっきの種類や素材によって処理内容は異なるので、興味がある方は、ぜひ自分でも調べてみると面白いでしょう!
コメント