「プラスチックの圧縮成形と真空成型ってどんな加工方法?」
「具体的な工程を教えてほしい」
「どういう特徴があって、どんな製品で使われるの?」
このような疑問を解決します。
こんにちは。機械設計エンジニアのはくです。
2019年に機械系の大学院を卒業し、現在はメーカーで機械設計エンジニアとして働いています。
本記事では、プラスチック成形の第4ステップとして「圧縮成形と真空成型の特徴」を解説します。
この記事を読むとわかること。
- 圧縮成形の仕組み・特徴・種類がわかる
- 真空成型の仕組み・特徴・種類がわかる
- 圧縮成形と真空成型の製品例がわかる
圧縮成形と真空成型は、似ているようで異なる成形方法。
簡単に言うと、つぶして成形するのが圧縮成形、吸い込んで成形するのが真空成型です。
今回は、そんな圧縮成形と真空成型の特徴を、図解でわかりやすく解説します。
射出成形との違いも紹介するので、ぜひ参考にしてください。
前回の記事はこちら。
圧縮成形とは
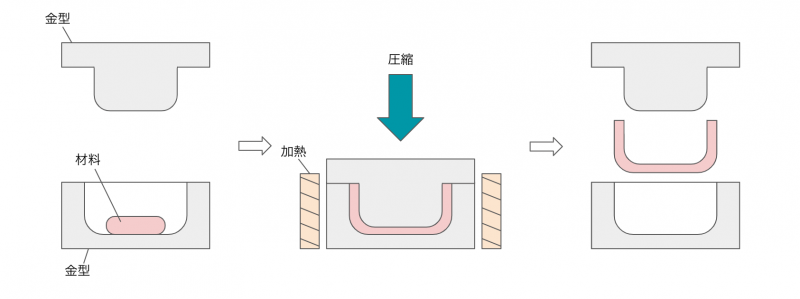
圧縮成形は、主に熱硬化性(加熱すると硬化する性質)プラスチックの成形に使われる方法です。
具体的な仕組みは上図のとおり。
まず、硬化する前のプラスチックを混ぜて粘土状にします。(粉末状や顆粒状の場合もある)
それを金型に入れ、加熱しながら圧縮していきます。
ちなみに、金型の温度は200℃程度。
すると、金型の中で反応が進み、プラスチック分子がつながっていきます。
反応終了後、金型を開いて成形品を取り出せば出来上がりです。
圧縮成形のメリット・デメリット
つづいて、圧縮成形の特徴として、そのメリット・デメリットを紹介します。
圧縮成形のメリット
- 装置・金型が安価
- 材料のロスが少ない
圧縮成形は、金型に材料を入れてつぶすだけなので、射出成形のように高圧で材料を流し込む必要がありません。
そのため、射出成形と比較して装置や金型製作のコストが安価に抑えられるのがメリットです。
また、射出成形では溶けたプラスチックの通り道(ランナー・ゲート)ができるため、これらを除去する必要があります。
一方で、圧縮成形ではこのランナーやゲートがないので、材料を無駄なく使えるのもメリットです。
圧縮成形のデメリット
- バリが発生しやすい
- 成形時にガスが発生する
圧縮成形では、金型に入れる材料の量が重要です。
具体的には、材料が少なすぎると金型の中ですき間ができてしまいますし、多すぎると圧縮時に材料がはみ出てしまいます。
たい焼きやたこ焼きを作るのをイメージすると、わかりやすいかもしれません。
はみ出た材料は製品としては不要なので、バリ取り作業が必要になります。
ちなみに、バリが発生しにくい圧縮成形として金型を閉じた状態で材料を送り込むトランスファー成形があります。
ただし、射出成形と同じく材料を送り込むために高い圧力が必要なので、機械や金型のコストが上がるのがデメリットです。
また、熱硬化性プラスチックは、反応して硬化する際にガスを発生させます。
ガスを放置しておくと、液化して金型に付着してしまうため、適切なガス抜きや定期的な金型の清掃が不可欠です。
真空成型とは
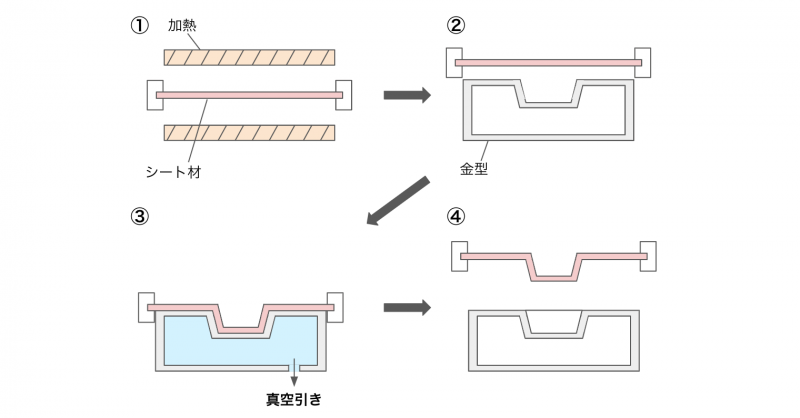
真空成型は、シート状のプラスチック材料を真空で型に吸い込んで成形する方法です。
圧縮成形とは違い、熱硬化性、熱可塑性(加熱すると柔らかくなり、冷却すると固くなる性質)プラスチックの両方に用いられます。
具体的な仕組みは上図のとおり。
まず、シート状のプラスチック材料を加熱して柔らかくします。
ただし、熱硬化性プラスチックの場合は高温にしすぎると硬化するので、ある程度柔らかくなるところでとどめます。
つづいて、柔らかくなったシートを空気が漏れないように型に固定します。
そして型の中を真空引きすると、シートが型に吸い込まれていきます。
型に密着しプラスチックが冷えると、固まって型の形状に成形されるのです。
真空成形でつくられる製品例としては、スーパーで売っている卵のパックや豆腐の容器、カップ麺の容器などがあります。
真空成型のメリット・デメリット
真空成形のメリット・デメリットとしては、以下が挙げられます。
真空成形のメリット
- 装置・金型が安価
- 大型品も成形できる
- 少量ロットに向いている
真空成形では、金型は片側だけあればOKであり、コストが安いのがメリットです。
大型品の成形も容易で、サイズが大きいほど金型も割安になります。
また、同じ型から成形した製品に後加工をすることで、形状違いの製品を簡単に製作できます。
したがって、試作や小ロット生産に向いているのも特徴です。
真空成形のデメリット
- 後加工が必要
- 型に当たらない部分の寸法精度が悪い
圧縮成形のバリ取りと同様、真空成形では不要な部分を除去する後加工が必要になります。
また、片側しか型に接触していないため、型に当たらない面は寸法精度がばらついてしまいます。
型に当たる面と当たらない面で冷却スピードも異なるので、肉厚や角部の形状が保証されないのもデメリットです。
このようなデメリットを解決する方法として、より大きな圧力で押し付ける圧空成形があります。
具体的に説明すると、真空で吸い込む側と反対側から圧力をかけて、シートを型に押し付ける方法です。
真空で吸い込む機構と圧力をかけて押し付ける機構の2つが必要になるため、少し複雑な構造になりますが、より大きい力でシートを型に密着させられるため、高精度な形状も成形できます。
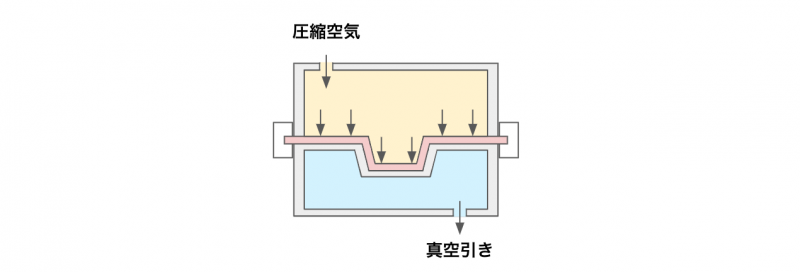
まとめ:つぶして作る圧縮成形と吸い込んで作る真空成型
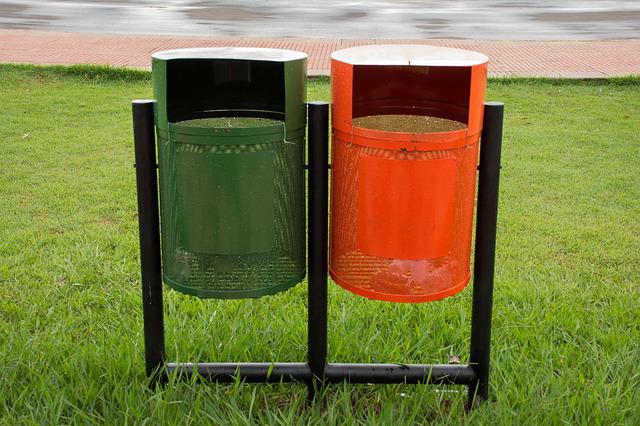
記事の内容をまとめます。
- 材料をつぶして成形するのが圧縮成形
- 真空で吸い込んで成形するのが真空成形
- 真空で吸い込み、圧力をかけて押し付けるのが圧空成形
- 圧空成形は、主に熱硬化性プラスチックの成形に使われる
- 真空成形は、熱硬化性・熱可塑性プラスチックの両方に使われる
- 圧縮成形も真空成形も、射出成形と違って金型が安価で製作コストが安い
- 成形後は、バリ取りや後加工が必要
- 圧空成形は、真空成形よりも高精度な加工ができる
以上です。
今回は、圧縮成形、真空成形、圧空成形という3つのプラスチック成形について解説しました。
身近な製品例だと卵のパックや食品の容器がありますが、ほかにも自動車のドアやインパネなどの成形に使われています。
もっと知りたいと思った方は、ぜひ自分でも調べてみると面白いでしょう!
コメント