「旋盤加工とはどんな加工方法?」
「どういう材料、形状、寸法の設計で使えるの?」
「設計する時の注意点や図面指示のポイントがあれば教えてほしい」
このような疑問を解決します。
こんにちは。機械設計エンジニアのはくです。
2019年に機械系の大学院を卒業し、現在は機械設計士として働いています。
本記事では、機械加工を学ぶ第1ステップとして「旋盤加工の特徴」をわかりやすく解説します。
この記事を読むとできるようになること。
- 旋盤加工とはどういう加工方法かがわかる
- どのような設計に使えるかがわかる
- 設計時の注意点と図面指示のポイントがわかる
旋盤加工は、機械加工の中でも材料を削って目的の形状に仕上げる「切削加工」の1つです。
一言でいうと丸形状に加工する際に使われますが、より早く・安く・精度良く仕上げるためにはいくつか注意点もあります。
今回は、旋盤加工の特徴から設計時の注意点をわかりやすく解説するので、ぜひ参考にしてください。
旋盤加工の特徴
さきほど言ったように、旋盤加工は丸形状に仕上げる加工方法です。
下図のように、回転する工作物に対して左から刃(バイトと呼ばれる)を当てて丸く削っていきます。
他の加工方法と違って、工作物を回転させるのが特徴です。

旋盤加工の最大のメリットは、早く・安く加工できること。
具体的に説明すると、たとえば角形状は面数が6面あるのに対し、丸形状なら外周と2つの端面の3面のみ。
したがって、加工が必要な面の数は丸形状が角形状の半分になり、その分早く・安く加工することができるのです。
さらに、長さを市販寸法に合わせて設計すれば、両端面を加工する必要もなくなり、1面のみで済むことになります。
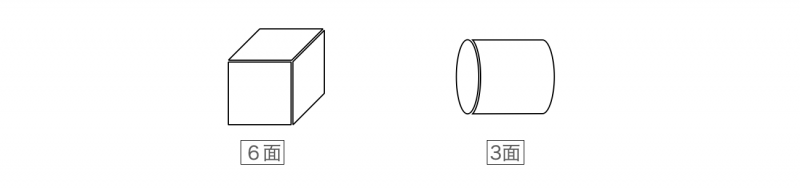
旋盤加工のもう1つのメリットは、外形が同じ部品を複数個つくるのに向いていることです。
外形が同じで長さが違う部品であれば、長めに加工して指定の寸法で切断していくことで、あっという間に複数の部品を加工することができます。
旋盤加工の種類
旋盤加工は、使用する刃の種類や刃の当て方を変えることで、単純な丸形状以外にも様々な加工が可能です。
①外周加工
外周加工では、単純な円柱加工(下図a)の他に、刃の当て方を変えることで直径が徐々に太くなるテーパー加工(下図b)ができます。
また、突切りバイトを使えば、途中に溝を入れる突切り加工(下図c)が可能です。
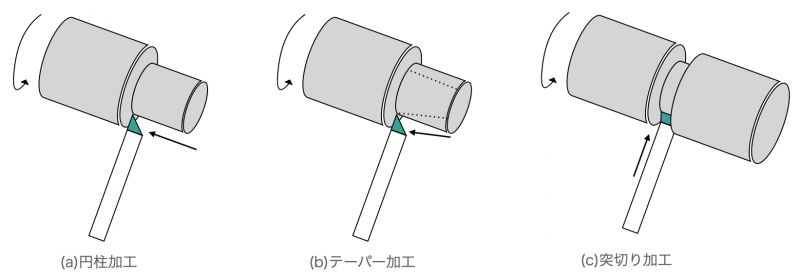
②端面加工
端面加工は、工作物の右側面にバイトを当てて端面を加工する方法です。
旋盤では材料の左側を固定して右端面を加工するため、左端面を加工したい場合は材料をいったんチャック(固定する器具)から外して左右を入れ替える必要があります。
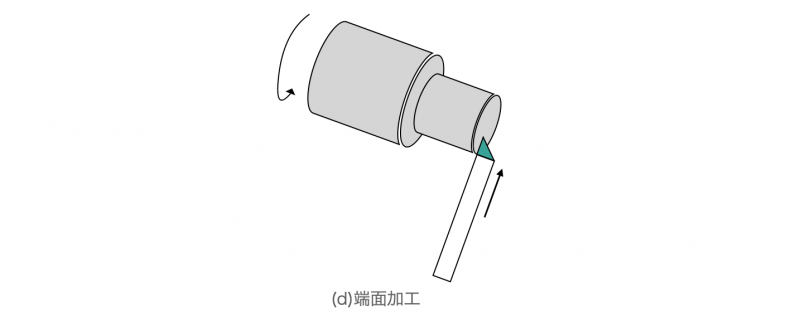
③穴あけ加工
バイトをドリルに変えれば、右側面に穴あけ加工ができます。
穴径が大きい場合や内面をキレイに仕上げたい場合は、ドリルで穴あけした後に中ぐりバイトを使って穴を広げる中ぐり加工が必要です。
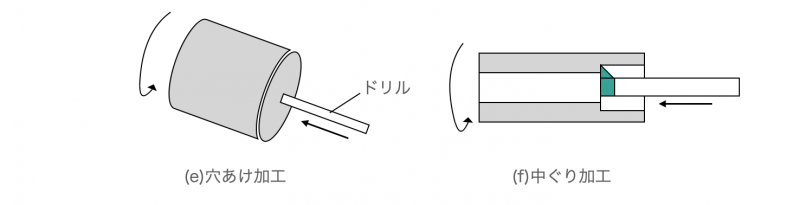
④ねじ加工
ねじ切りバイトを使えば、図のようにおねじ加工ができます。
また、ドリルで穴あけした後にめねじ切りバイトを使えば、めねじ加工も可能です。
ねじ切り加工は,一般にタップやダイスと呼ばれる器具を使って行いますが、大きい径や特殊なねじを切る場合は、このように旋盤を使って加工することができます。
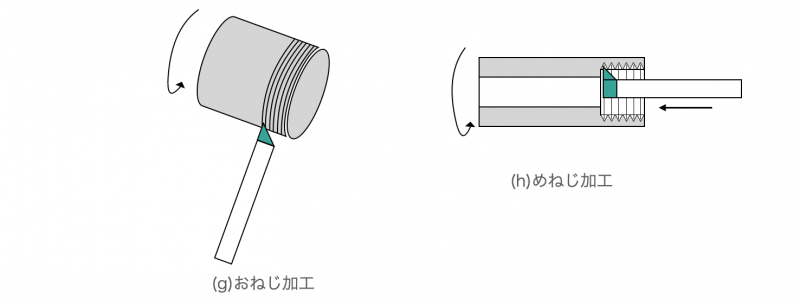
旋盤の加工条件
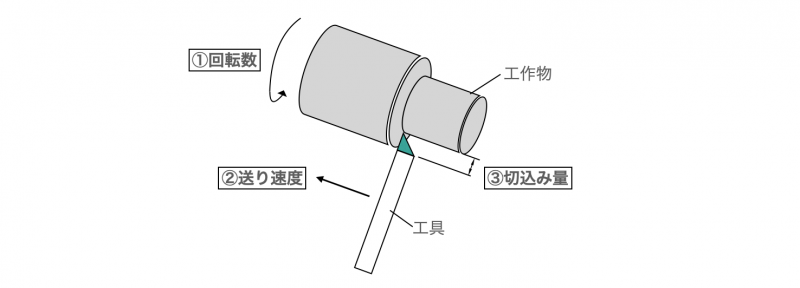
旋盤加工における品質(Quality)・コスト(Cost)・納期(Delivery)は、下記3つの条件によって決まります。
ここで言う品質は寸法や表面粗さなどの仕上がり精度のこと、コストはそのまま加工費のこと、納期は加工にかかる時間のことです。
- 工作物の回転数
- バイトの送り速度
- バイトの切込み量
①工作物の回転数
旋盤では、工作物を回転させバイトを前後左右に動かすことで加工します。
工作物の回転数によって切削速度(1分間に切り取る長さ[m/分])が変わり、部品の仕上がりや工具の寿命に影響します。
基本的に、切削速度が速いほど短時間で加工でき、加工面もキレイに仕上がります。
しかしながら、切削速度を上げるとバイトの摩耗が激しくなるため、工具の寿命は短くなります。
したがって、実際の加工では加工効率と経済面から、最適な切削速度を算出して加工しています。
②バイトの送り速度
工作物が1回転した時にバイトが移動する量を送り量と言います。
単位は[mm/回転]です。
「送り量(mm/回転)」にさきほどの「工作物の回転数(回転/分)」をかけると、バイトの「送り速度(mm/分)」が求まります。
送り速度を上げると加工効率は上がりますが、加工の表面は粗くなります。
③バイトの切込み量
バイトが工作物を削り取る深さが「切込み量(mm)」です。
具体的に言うと、一度にたくさん削るのか、少しだけ削るのかということ。
切込み量が大きいと、当然切削回数が減って加工効率は上がりますが、加工精度は粗くなります。
したがって、実際の加工では、切込み量が大きい粗加工のあとに、切込み量を小さくして仕上げ加工を行うのが普通です。
設計時の注意点と図面指示のポイント
さいごに、旋盤加工を使って部品を設計する際の注意点と図面を書く時のポイントを紹介します。
部品が加工できない・精度が保証できないといったトラブルを起こさないためにも、きちんと理解しておきましょう。
①加工の向きに合わせてビューを配置する
最初に言ったように、旋盤は工作物の左側を固定して、右側から刃を当てて加工していきます。
したがって、図面を書く際はこの加工の向きに合わせてビューを配置するのが、加工者にとって「やさしい図面」です。
具体的には、下図のような左側が細くなる段付き形状や、左側の穴径が大きい穴あけ加工は、右向きに加工できるように配置しましょう。
また、部品を縦向きに配置するのも加工の向きと異なるのでNGです。
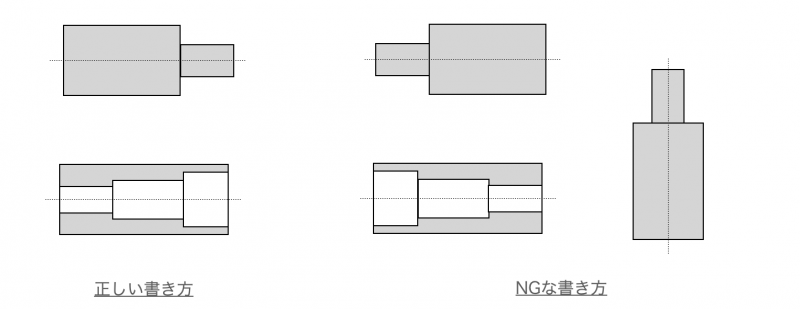
②すべての加工が右側からできる形状にする
下図のように両端に止まり穴(貫通していない穴)があると、穴Aを加工したら一度工作物をチャックから外して回転させ穴Bを加工するといった作業が必要です。
しかしながら、これだと加工の手間が増えますし、穴AとBの中心軸がずれてしまう可能性があります。
したがって丸形状では、一度固定したら向きを変えない形状、すなわちすべて右側から加工できる形状で設計するのが好ましいです。
これによって加工の手間やコストを削減でき、中心軸のずれも発生しないので加工精度も上がります。
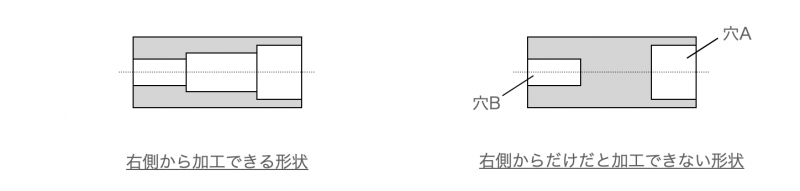
③隅部にR形状がつくことを考慮する
切削加工では、工具の形状がそのまま工作物に転写されます。
工具は先端が尖っているように見えて微小なR形状がついているため、実際の加工では隅部にこのRが転写されるのです。
たとえば旋盤では、段付き形状の隅部にRがつきます。
ここで、隅部を「R0.5」のように指定すると、使用する工具も先端(ノーズ半径)がR0.5のものに限定されてしまいます。
しかしながら、このノーズ半径は加工効率や精度に影響するため、設計段階では加工者が選択できるように範囲を広げておくのが望ましいです。
図面に「R0.5以下」と書いておけば、加工者はノーズ半径が0〜0.5の工具の中から選択できるので、より効率よく加工することができます。
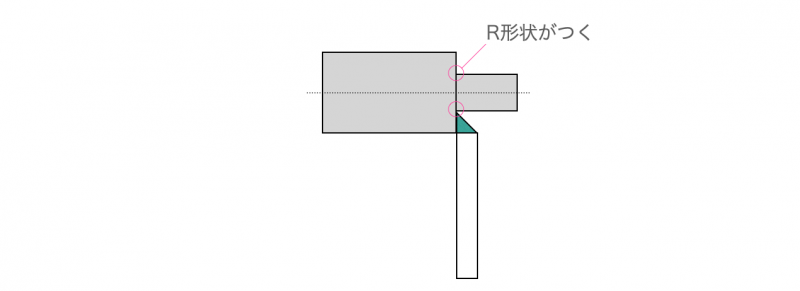
④工作物が長い時は「センタ穴可」としておく
直径に対して工作物が長い、いわゆる細長い丸棒形状だと、先端が垂れて軸がずれる可能性があります。
この対策として、右端面にセンタ穴加工をして支える方法があります。
しかしながら、右端面に仕様とは関係のないセンタ穴が開いてしまうため、これをする場合、加工者はセンタ穴加工の可否を設計者に確認しなければいけません。
一方、あらかじめ図面に「センタ穴可」と記載しておけば、加工者が確認する手間が省けます。
目安として、工作物の長さが直径の4〜5倍になる時は、「センタ穴可」の指示を追記するといいでしょう。
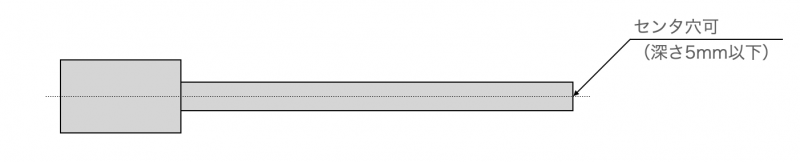
⑤おねじ・めねじの逃げ加工
おねじの不完全ねじ部は、谷径が徐々に小さくなる難しい加工です。
そこで、下図のように逃げ加工をしておくと、通常のねじ加工だけで済むのでより簡単に加工することができます。
逃げ加工の幅は2ピッチ、深さは谷径より小さくするのが目安です。
同様に、めねじ加工でも穴の先端部分には、バイトを逃がすための逃げ加工が必要になります。
こちらも逃げ寸法は2ピッチ以上が目安です。
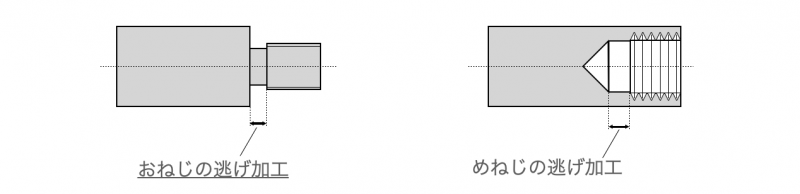
工具の面取り部や食い付き部などによってできる山形が不完全なねじ部のこと。
「ねじ」としての機能を持たないため、不完全ねじ部と呼ぶ。
まとめ:旋盤加工の特徴を理解して「やさしい設計」を心がけよう
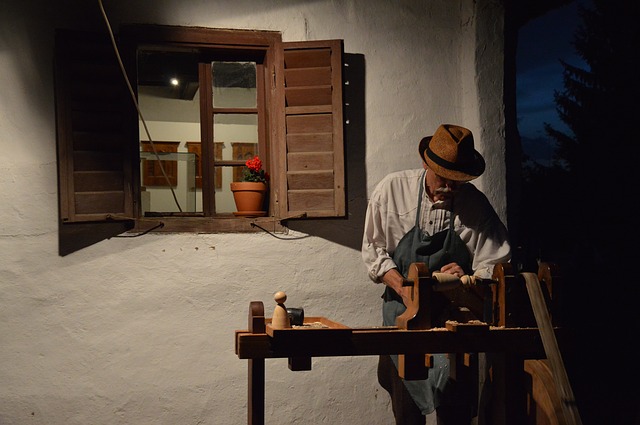
以上、旋盤加工の種類と特徴、設計時の注意点をまとめました。
旋盤加工は、機械加工の中でもよく使われる加工方法の1つです。
初心者は、加工方法をきちんと理解せずに適当な図面を書いてしまいがちですが、これだと精度の悪化やコスト・納期の増加につながりかねません。
機械設計初心者の方は、今回紹介した内容をきちんと理解して、加工者に「やさしい設計」ができるように心がけましょう。
コメント